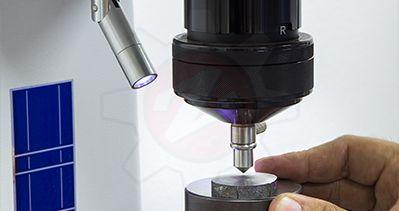
Pomiar twardości metali
Zetech oferuje wykonywanie pomiaru twardości metali za pomocą profesjonalnego i bardzo precyzyjnego oprzyrządowania. Właściwa twardość elementów gwarantuje ich wydajne i bezawaryjne działanie, zgodne z zamierzeniem projektanta maszyny. Kontrola odtworzenia prawidłowej twardości każdego istotnego detalu ma znaczenie szczególnie przy urządzeniach, których demontaż jest skomplikowany, a awaria może prowadzić do uszkodzenia również innych podzespołów. Pomiar twardości metalu jest zalecany szczególnie w przypadku wykonywania ulepszenia cieplnego, np. hartowania.
Znaczenie pomiaru twardości metali
Pomiar twardości metali ma często decydujące znaczenie o użyteczności podzespołu czy detalu do konkretnego zastosowania. Twardość metalu, z jakiego wykonano element, decyduje o wielu jego parametrach użytkowych – tendencji do odkształcania się pod wpływem działających sił, wytrzymałości na udary oraz trwałości. W przypadku elementów, które ze sobą współpracują, często istnieją różne wymagania co do twardości obu elementów i ich wytrzymałości. Na przykład w przypadku kół jezdnych suwnic i szyn, twardość materiału użytego do produkcji kół powinna być o 20% wyższa niż szyn, ponieważ taki stosunek parametrów gwarantuje optymalny poziom zużycia obu elementów. Istnieje wiele podobnych sytuacji, w których dobór twardości elementów przesądza o ich wzajemnym oddziaływaniu na siebie i tempie zużycia czy nawet ryzyku awarii.
Zapewnienie odpowiedniej twardości metalu, poza innymi parametrami dotyczącymi wymiarów czy właściwego rodzaju materiału, może mieć kluczowe znaczenie dla urządzeń, gdzie poszczególne elementy pracują z dużymi obciążeniami. Jest to ważne szczególnie, jeśli awaria mogłaby wywołać dłuższy przestój, np. w przypadku remontu przekładni zębatych. Współpracujące ze sobą wałki czy koła zębate o różnej średnicy i ilości zębów działają w nich pod dużym obciążeniem. Precyzyjne ustalenie stosunku twardości obu elementów może przesądzać o ich podatności na zmęczenie i uszkodzenie. Regeneracja elementów wymaga więc pieczołowitego odtworzenia również podatności na odkształcenia odtwarzanego elementu.
Metody pomiaru twardości metali
Najpowszechniej stosowanymi metodami pomiaru twardości metali są metody statyczne – Vickersa, Brinella oraz Rockwella. Polegają one na oznaczeniu poziomu oporu stawianego przez materiał przy próbie jego odkształcenia za pomocą wgłębnika.W przypadku metody Vickersa wgłębnik ma kształt ostro zakończonego ostrosłupa czworobocznego o wierzchołku z kątem 136°. Dla wyznaczenie wyniku – współczynnika twardości Vickersa HV – mierzy się długości przekątnych czworobocznego wgłębienia w powierzchni próbki.
W metodzie Brinella na badany materiał oddziałuje wgłębnik w kształcie kulki. Dla sprawdzenia twardości metalu mierzy się średnicę powstałego wgłębienia i ze specjalnego wzoru wyznacza współczynnik twardości Brinella HBW.Badanie twardości metodą Rockwella (HR) polega na dwustopniowym nacisku na powierzchnię przy użyciu wgłębników – ze stożkiem o podstawie czworokątnej lub zakończonego kulką o średnicy 1,588 mm albo 3,175 mm. Rodzaj wgłębnika jest uzależniony od skali, na której przeprowadza się badanie. Wynikiem jest przyrost głębokości uzyskanego odkształcenia.